ABOUT US
Numerical Analysis Technology
- Hydrodynamic lubrication analysis
- Machine Learning Approach to Predicting Pressure Distribution in Hydrodynamic Lubrication
- Multi-objective optimization of surface texture shapes based on genetic algorithms
- Elucidation of sliding mechanism by computational science
- Deep groove fluid dynamics analysis
- Thermo-fluid dynamics analysis technology
Hydrodynamic lubrication analysis
Hydrodynamic lubrication analysis technology is a simulation technique that solves one of the fundamental equations in the field of tribology, called the Reynolds equation. This technology is mainly used to predict the performance of mechanical seals with surface texturing, and can calculate key indicators such as frictional resistance and suction/leakage rate.
Hydrodynamic lubrication analysis technology is one of Eagle Industry’s core technologies that led to the development and commercialization of the “world’s first mechanical seal with both minimizing leakage and low torque,”
and we continue to engage in friendly competition with world-class research institutions and companies.
Combined with numerical optimization methods, it enables us to efficiently derive the optimum texturing shape for each operating environment and condition.
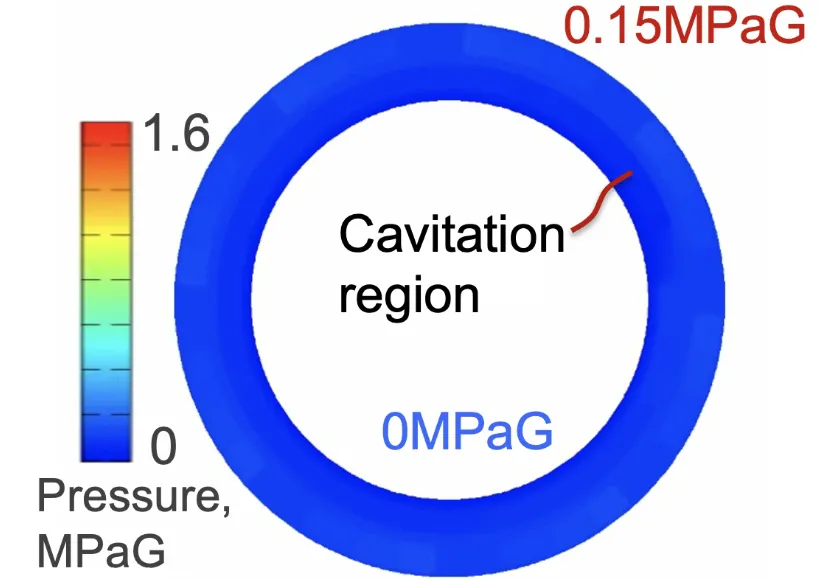
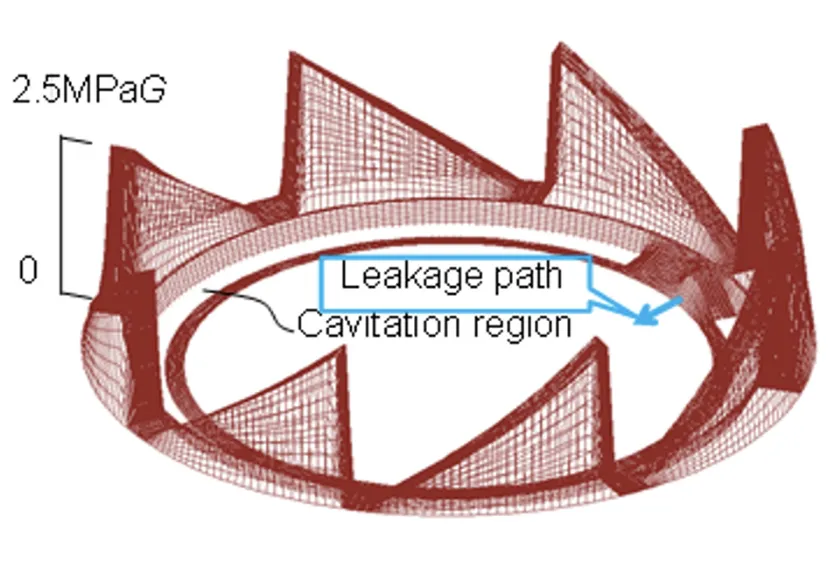
Machine Learning Approach to Predicting Pressure Distribution in Hydrodynamic Lubrication
The pressure distribution generated by the surface texture is calculated based on hydrodynamic lubrication theory and contributes to improved sealing and lubrication. Since the operating conditions differ from customers, the surface texture geometry is optimized for each application. In the process, a large amount of analytical data is generated. By learning these data through machine learning, which has become a hot topic in recent years, we have verified the construction of a surrogate model that can replace numerical analysis. By employing “U-Net,” which is commonly used for colorization of black-and-white images, as a machine learning model, we succeeded in constructing a surrogate model that can reproduce the pressure distribution from numerical analysis with high speed and accuracy based on the surface texture shape. By utilizing accumulated data through machine learning and supporting numerical analysis, the computing time required for numerical analysis can be significantly reduced.
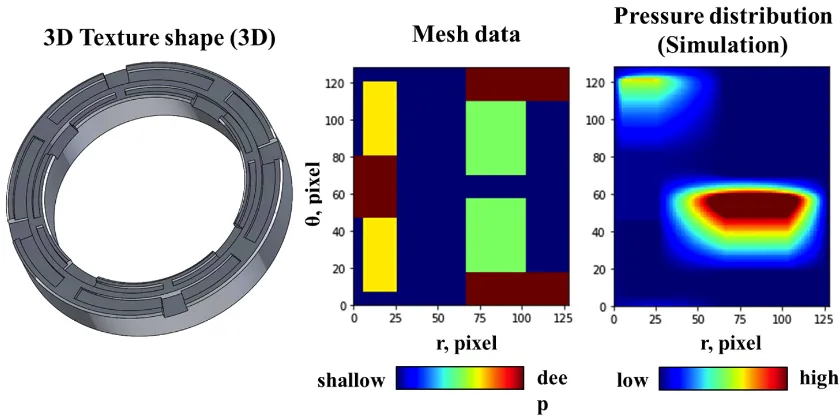
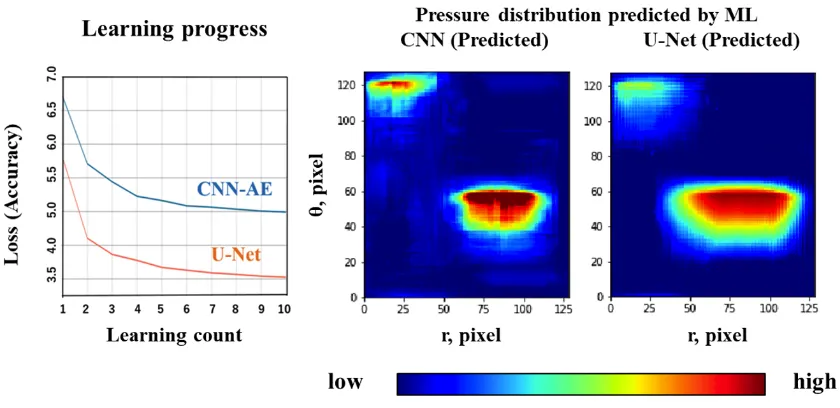
Multi-objective optimization of surface texture shapes based on genetic algorithms
Surface texturing can be designed in a great variety of ways by combining different groove geometries. However, in order to adapt to environments with a wide variety of fluids and operating conditions, it is necessary to demonstrate excellent properties for a large number of evaluation items. The number of studies required to evaluate each groove shape is enormous, and the complexity of the design indexes becomes an issue. Eagle Industry uses a genetic algorithm for multi-objective optimization to efficiently design appropriate groove shapes for a large number of design indexes. The genetic algorithm first evaluates multiple randomly formed solids (surface texturing) and searches for superior groove features. In the next generation, a group of solids inheriting the superior groove features are formed and further superior groove features are searched for. By repeating the generation change, it is possible to search for more superior individuals and calculate the optimum surface texturing for various evaluation indices.
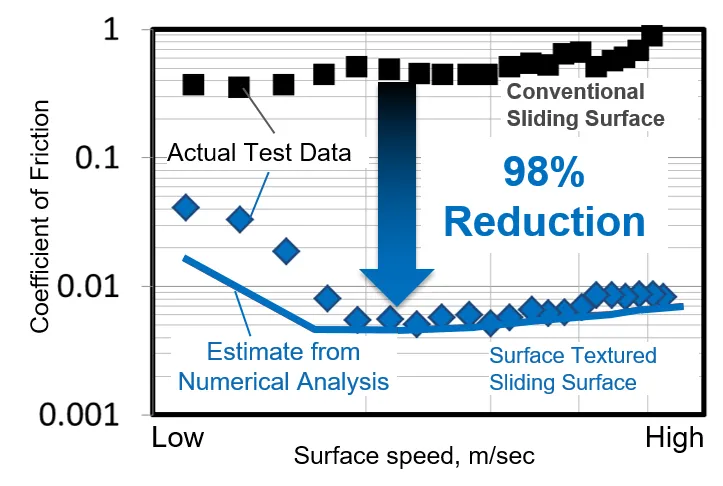
Elucidation of sliding mechanism by computational science
Ceramics such as carbon and SiC are used in the sliding parts of mechanical seals. Wear particles generated by the sliding of these materials and the formation of nanointerfaces are very important in reducing frictional resistance and ensuring stability during long-term operation. Eagle Industry utilizes computational chemistry, as typified by molecular dynamics simulations, to elucidate the mechanisms of these phenomena and to design material compositions suitable for sliding. Computational chemistry enables theoretical verification at the molecular and atomic level, independent of the designer’s sensitivity. Eagle Industry uses a relatively large model (50,000 atoms) to simulate the sliding between substrates, allowing analysis of the formation process of tri-block films and the composition of the wear powder generated by the sliding. It is also possible to qualitatively explain changes in the coefficient of friction due to differences in the atmosphere and composition of the substrates.
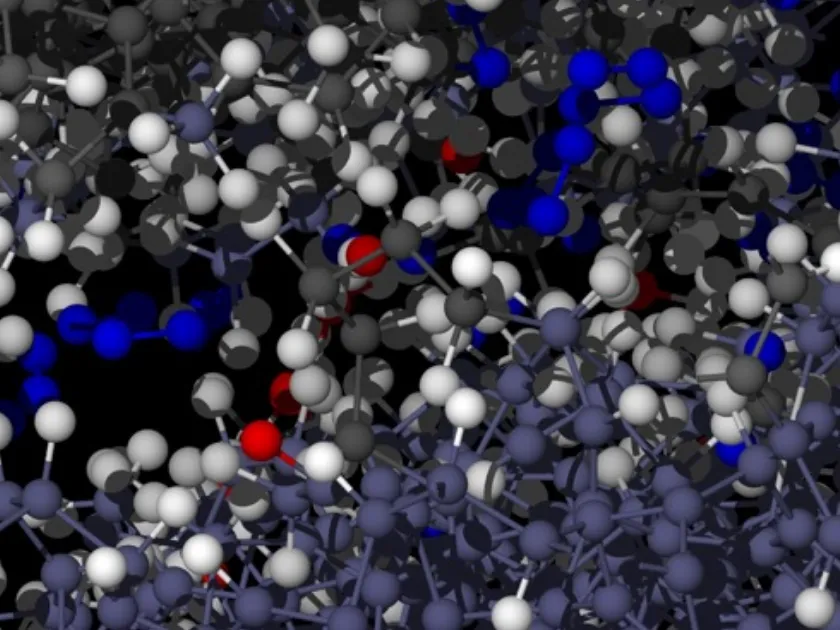
Deep groove fluid dynamics analysis
In Eagle Industry’s surface texturing technology, the sliding surfaces of mechanical seals are sometimes given fluid inlet grooves to introduce and effectively utilize fluids. For these types of textured geometries, predicting and evaluating the complex flow inside the groove is critical to ensuring lubricity.
Eagle Industry uses Computational Fluid Dynamics (CFD) to predict and visualize the flow inside the above grooves, and can propose groove designs that are appropriate for the operating environment and conditions, as well as groove shapes that fit various environments.
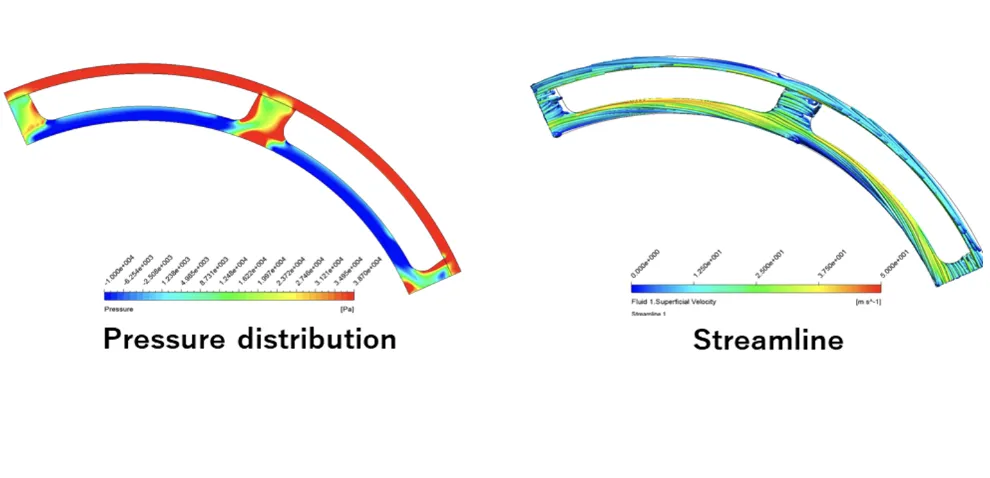
Thermo-fluid dynamics analysis technology
Eagle Industry is actively promoting CAE (Computer Aided Engineering), a technology that can greatly contribute to cost reduction, shorter delivery times, and higher quality by predicting information that is difficult to measure and reducing the number of tests.
Thermo-fluid dynamics analysis technology (coupled thermo-fluid dynamics analysis) is a technology that can predict fluid behavior and heat transfer in an integrated and accurate manner by simultaneously solving conservation laws for energy, momentum, and mass of the fluid and structure. It is an important analysis technology in fields where heat generation and heat absorption have a large impact on the entire system, and contributes greatly to improving the quality and cost reduction of EKK products.
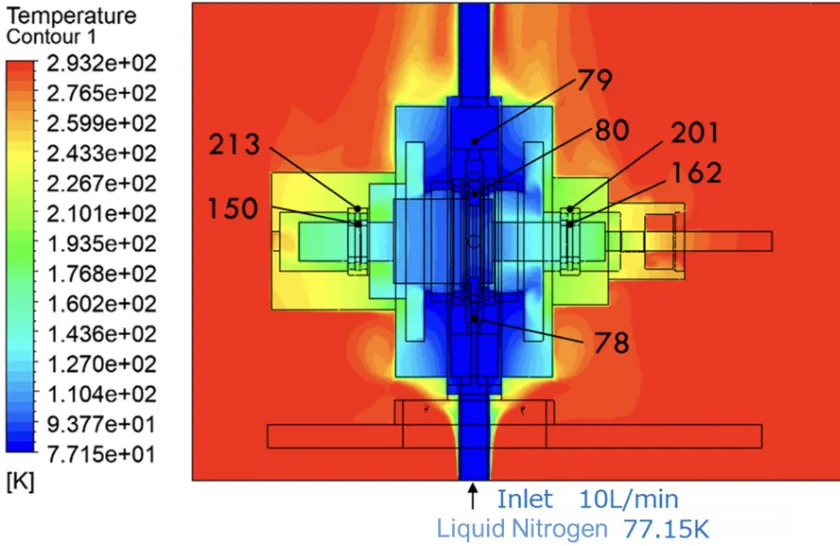